Overcoming silos in the ceramics industry
Professor Ian M Reaney FIMMM, Director of the Transforming Foundation Industries Network+, calls for greater synergy with universities to decarbonise the UK ceramics industry.
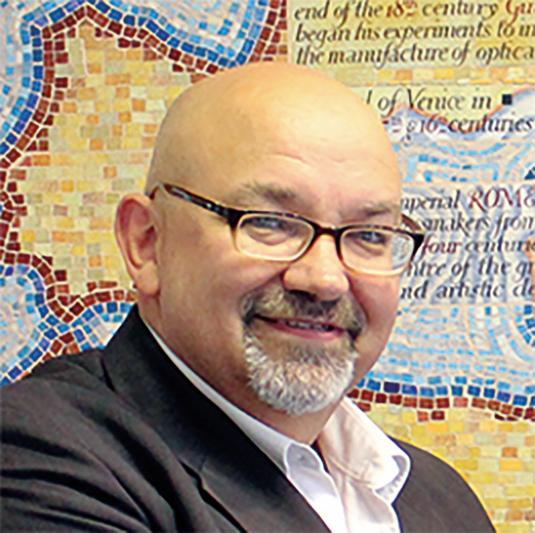
In the UK, ceramics is considered one of the six Foundation Industries (ceramics, cements, paper, glass, chemicals and metals). The global market for ceramics is estimated to increase by 5.2% by 2030, reaching approximately US$0.4trln, according to a report by Grand View Research, Inc, USA.
The ceramics sector may be broadly separated into traditional ceramics (tableware, sanitaryware), construction materials (clay bricks and tiles), and advanced, technical and electro-ceramics (e.g. ZrO₂, Al₂O₃, Al₂O₃-SiO₂ refractories, and BaTiO₃).
Traditional ceramics and construction materials are multiphase, principally based on cheap raw materials such as kaolin clay, densified by viscous composite sintering, and low cost at per-unit volume. They constitute more than 90% of the world’s ceramic production and depend almost exclusively on methane-burning continuous kilns.
High-temperature Al₂O₃-SiO₂ refractories fall into the category of technical ceramics but also use gas furnaces in the manufacture of thermal bricks and castables. The large capital expenditure of replacing legacy equipment for these industries means that an informed choice of next-generation power/fuel source is critical.
Advanced and electro-ceramics are mainly manufactured using electric batch or continuous furnaces. Therefore, as the national grid becomes decarbonised through increased use of renewables and nuclear power, the manufacture of advanced and electro-ceramics will approach net-zero at least in production (mining and refining of raw materials is mainly performed outside the UK). Innovation to improve performance, reduce raw materials costs and embodied energy will still be required, but advanced and electro-ceramics are currently and, in the future, unlikely to be a significant contributor to climate change based on the volumes produced and the methods of manufacture, respectively.
However, within the UK Engineering and Physical Sciences Research Council ceramics’ portfolio (~£100mln), advanced and electro-ceramics receive the most funding. This generates much excellent research leading to reduced manufacturing/energy costs and new products, but it does not have a significant impact on the carbon footprint of the sector as a whole.
The path to net-zero for traditional and construction ceramics is complex and not only requires ‘fuel switching’ to an appropriate energy source, but also extensive research to improve resource and energy efficiency of production to remain competitive, as carbon offset targets become increasingly stringent.
There has never been a greater need therefore for collaboration between the ceramics industry and the academic community on a wide range of technical topics such as the i) development of net-zero carbon furnaces, ii) lightweighting and materials substitution, iii) energy recovery, iv) recycling of waste destined for landfill and v) increasing digitisation, sensing and control systems to minimise wastage.
Worryingly, ceramics – like many of the Foundation Industries – is failing to attract younger employees and those with protected characteristics.
To actively encourage greater R&D and ultimately secure funding to de-risk and drive innovation towards net-zero, several key steps are required such as i) the formation and/or participation in networks designed to establish shared best practice on resource efficiency, energy efficiency and decarbonisation; ii) greater engagement in the traditional and construction ceramics by the academic community; iii) greater engagement with furnace manufacturers in the design of next-generation furnaces; iv) a willingness to participate in consortia to secure large scale-funding; v) and greater general awareness among Technical Directors and CEOs, particularly in smaller companies, of available potential funding such as Knowledge Transfer Partnerships and the Industrial Strategy Challenge Fund.
Engagement with academia, from undergraduates to faculty, would also help secure a pipeline of diverse young talent to help drive innovation in the ceramics sector.
A continued ‘silo’ approach unwittingly adopted by academics and industrialists alike is a death sentence for the UK ceramics industry. Academia has expertise and an equipment base vital to establish the understanding to make a company’s product portfolio more sustainable, and equally without an indigenous industry, funding for ceramic research will go into decline.
There is much to be mutually gained by enhancing cooperation, and increasingly there are platforms that can enable connections. The main purpose of the Transforming Foundation Industries Network Plus is to make such links, encourage collaboration and fund proof-of-concept R&D.
The EconoMISER grant has given research technology organisations, in addition to the Royce Institute and Lucideon, a platform of state-of-the-art equipment for R&D. The Transfire Hub has a remit to undertake research in resource and energy efficiency within the Foundation Industries, and the British Ceramic Confederation can help with partners for consortia and lobby government on critical initiatives.
The task to decarbonise seems overwhelming for individual ceramic companies, but a de-risked collaborative approach is cost effective and efficient. Academics chase ‘high impact factor’ research to enhance career progression and aid in the Research Excellence Framework (REF) audit, but a balance of industrially led and blue skies research is essential, or we risk losing the very sector that encourages UK Research and Innovation to maintain its funding portfolio in ceramics.